Lean Transformation of Admin Systems in South Sudan
At Coalition for Humanity’s South Sudan office, inefficient administrative systems were slowing down critical operations. Staff faced significant delays when processing basic procurement and HR actions due to overly complex workflows that required more than five levels of approval. These delays affected everything from purchasing essential supplies to onboarding urgently needed staff. Meanwhile, disorganized filing systems and cluttered workspaces made it difficult for team members to locate documents, complete routine tasks, or train new hires effectively. These inefficiencies not only drained time and resources but also risked undermining the delivery of humanitarian programs.
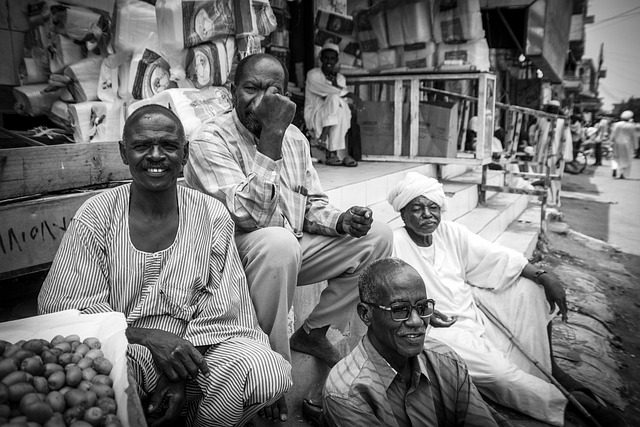
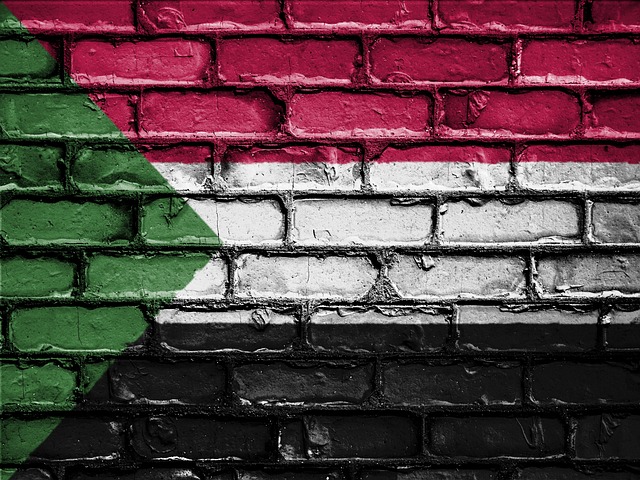
A root cause analysis revealed that departmental workflows lacked standardization and were based on informal, undocumented practices. Legacy systems were still in place, and Lean principles were virtually unknown across the organization. Staff often relied on memory or peer instruction to complete administrative processes, contributing to errors and repeated steps. The physical office layout—including filing zones—lacked intentional structure, further compounding delays and onboarding confusion.
To address these challenges, the team launched a Lean-driven improvement initiative targeting HR, procurement, and logistics functions. Core workflows were mapped and reviewed using Lean tools to identify non-value-adding steps. As a result, procurement approvals were reduced from five or more to just one, significantly accelerating turnaround time. Filing systems were reorganized with clear, visible labels to simplify navigation and access to key documents. The team embedded Lean reminders into quarterly operations memos and created short training refreshers to reinforce new processes. These efforts were further supported by peer-to-peer learning, with staff informally training one another and spreading Lean concepts across departments.
The outcomes were transformative. Hiring and procurement cycles became faster and less error-prone. Team members could now find documents more easily and complete routine tasks with greater autonomy, reducing dependence on senior staff. Onboarding of new hires became smoother thanks to clearer workspace organization and documentation. While precise KPIs such as time-to-hire or supply lead time were not centrally tracked, teams reported noticeable improvements in responsiveness and efficiency.
The Lean methodology is now becoming part of the organization’s operating DNA, spanning operations teams from HR and logistics to finance. The initiative has also sparked broader interest: the approach is being viewed as a model for other national NGOs operating in South Sudan. Leadership buy-in is growing, with plans underway to train senior management to further institutionalize Lean practices across the organization.